Neutral hardening heat treatment is primarily used to increase the hardness and strength of steel components. The process is carried out in an atmosphere that doesn't alter the chemical composition of the surface. The parts are usually heated in a neutral atmosphere using protective gasses like Nitrogen or a mixture of gases in a controlled furnace to avoid the oxidation or carburization.
Industries Served:

Defense Industry

Gears Industry

Fasteners Industry

Forging Industry
Material Grades That Can Undergo The
Neutral Hardening
Material
Alloy Steel, Carbon Steel, Tool Steel
Material Grade
AISI 4140, 4340, 8620, 9310, AISI 1045, AISI 1050, AISI D2, AISI M2
Neutral Hardening Furnaces
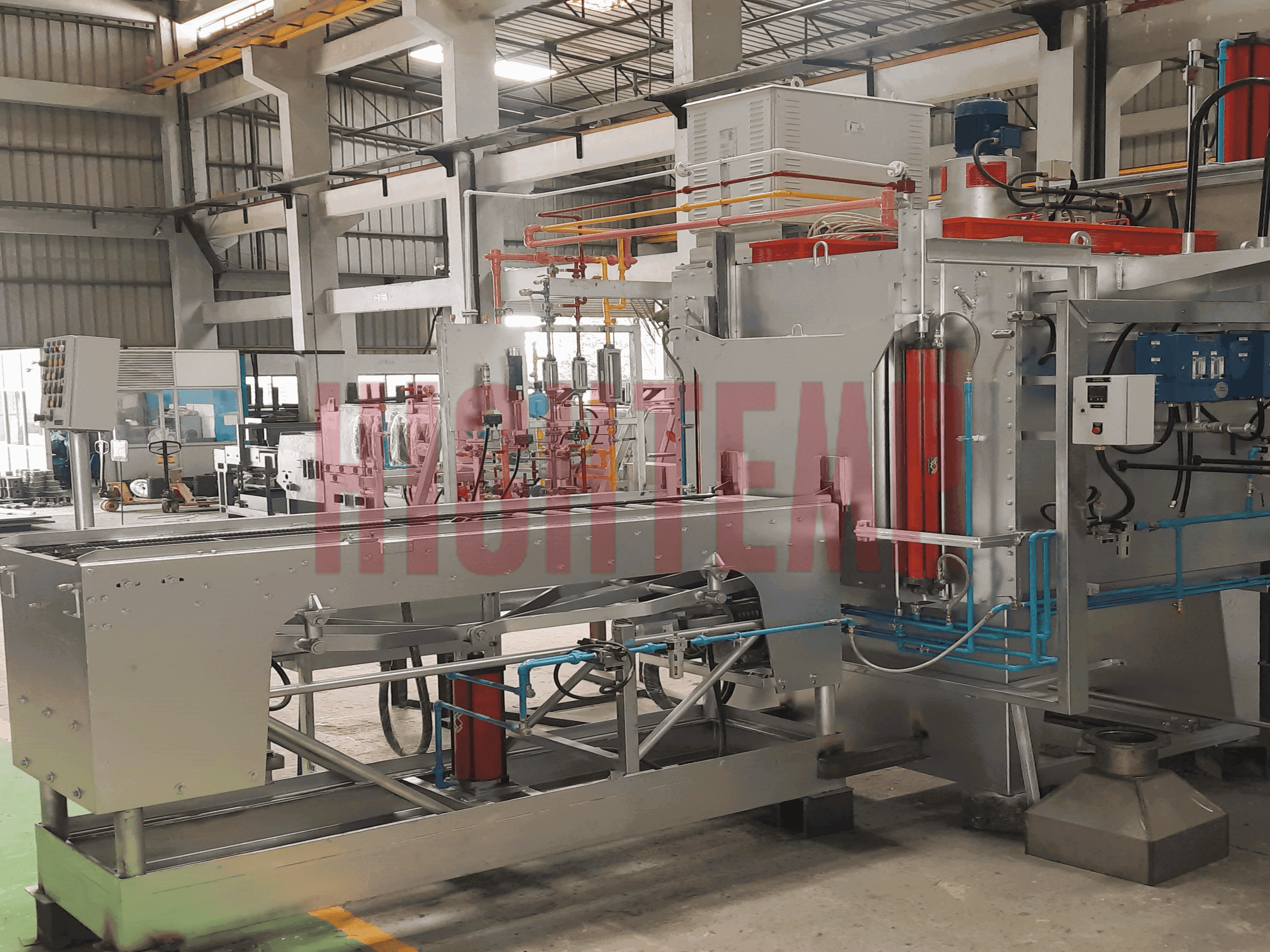
TKM 40
A sealed quench furnace is a highly efficient, controlled atmosphere furnace designed for heat treatment processes such as hardening and tempering. It is widely used in the automotive and industrial sectors for components requiring superior mechanical properties and wear resistance. For the heat treatment of engine components such as connecting rods and valves made from materials like 4130, 4340, 42CrMo4, En-8D, A217, and A351 Hardening and Tempering process is implemented where the components are heated to their austenitizing temperatures in a controlled atmosphere to prevent oxidation and decarburization. Rapid quenching in oil or polymer quenchants, to achieve desired hardness and microstructure. Components are further reheated below the critical temperature to achieve the required toughness, ductility, and stress relief. This furnace can perform other heat treatment processes, including carburizing, , carbonitriding, normalizing, nitrocarburizing, nitriding, austempering, neutral hardening, annealing, and bright hardening..
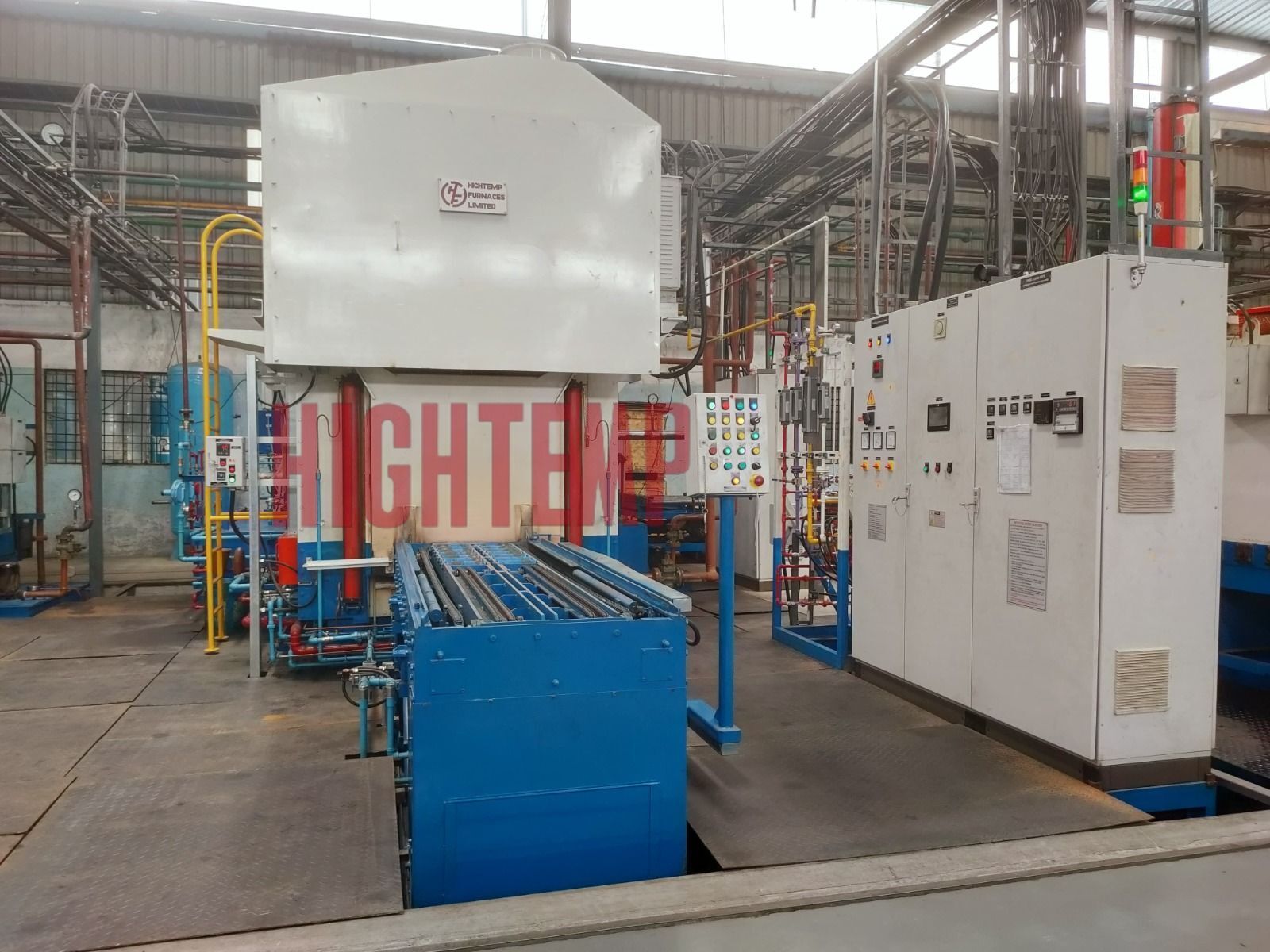
TKM 120
The Sealed Quench Furnace is a high-performance heat treatment system designed for austempering, carburising, and tempering. Ideal for components like gears, shafts, clutch plates, springs, fasteners, and crankshafts, it delivers superior wear resistance, toughness, and fatigue strength. Austempering is a specialized process that transforms steel into an ausferrite microstructure, enhancing toughness, wear resistance, and fatigue strength with minimal distortion. This makes it ideal for components that require superior mechanical performance. This furnace can perform other heat treatment processes, including hardening, carbonitriding, normalizing, nitrocarburizing, nitriding, neutral hardening, annealing, and bright hardening.
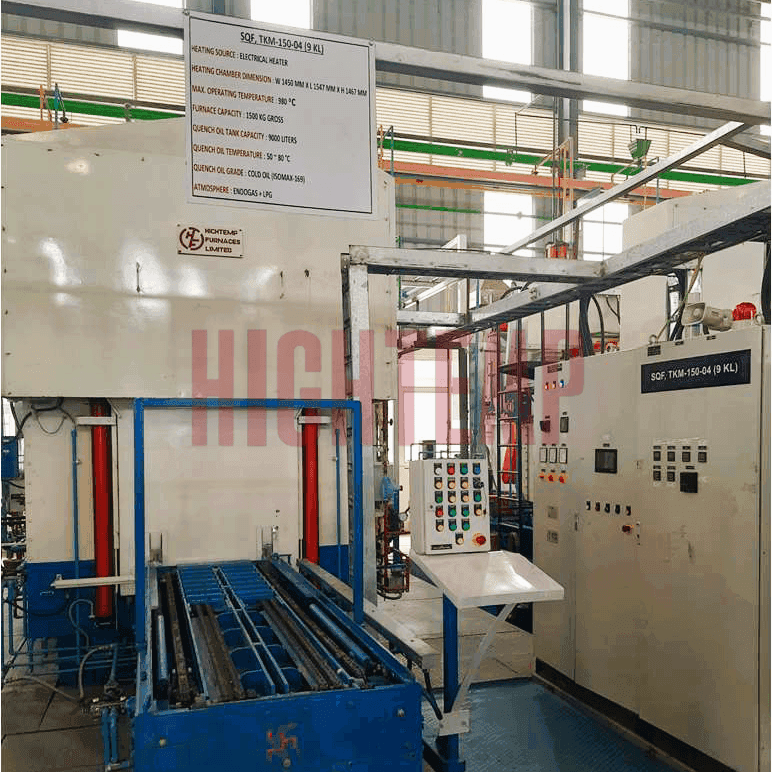
TKM 150
The Sealed Quench Furnace is compatible for heat treatment of material grades like EN8, EN9, EN31, 16MnCr5, 20MnCr5, SAE 4140, and SAE 8620. This furnace ensures precise atmosphere control and uniform heating for consistent results. Whether strengthening automotive gears or hardening industrial tools, it excels in enhancing mechanical properties while minimizing distortion. In this Tempering is a crucial step that follows processes like carburising or case hardening, designed to relieve internal stresses, reduce brittleness, and enhance the overall toughness of components. Similarly, Austempering process ensures an optimal balance between hardness and ductility, making treated parts more durable and resistant to impact. This furnace can perform other heat treatment processes, including hardening, carbonitriding, normalizing, nitrocarburizing, nitriding, austempering, neutral hardening, annealing, and bright hardening.
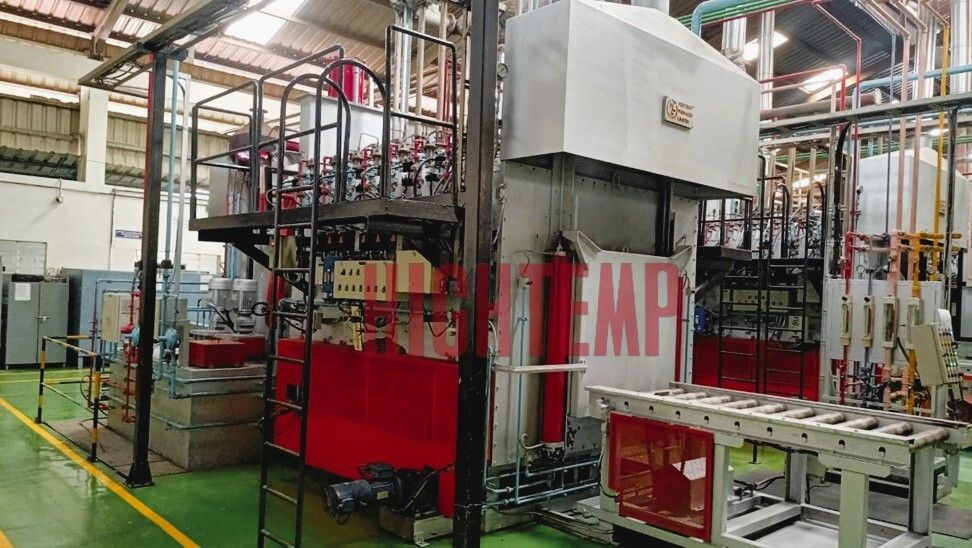
TKM 250
Carburising in a Sealed Quench Furnace is a highly efficient and controlled process that enhances the surface hardness of low-carbon steel components. By diffusing carbon atoms into the surface, this process creates a hard, wear-resistant outer layer while retaining a tough, ductile core. The sealed quench furnace ensures a precisely controlled carbon-rich atmosphere and uniform heating, resulting in consistent and high-quality results. Widely used in automotive, aerospace, and heavy machinery industries, carburising in a sealed quench furnace delivers superior mechanical performance, extended component life, and reliable results for demanding applications. This furnace can perform other heat treatment processes, including tempering, hardening, carbonitriding, normalizing, nitrocarburizing, nitriding, austempering, neutral hardening, annealing, and bright hardening.
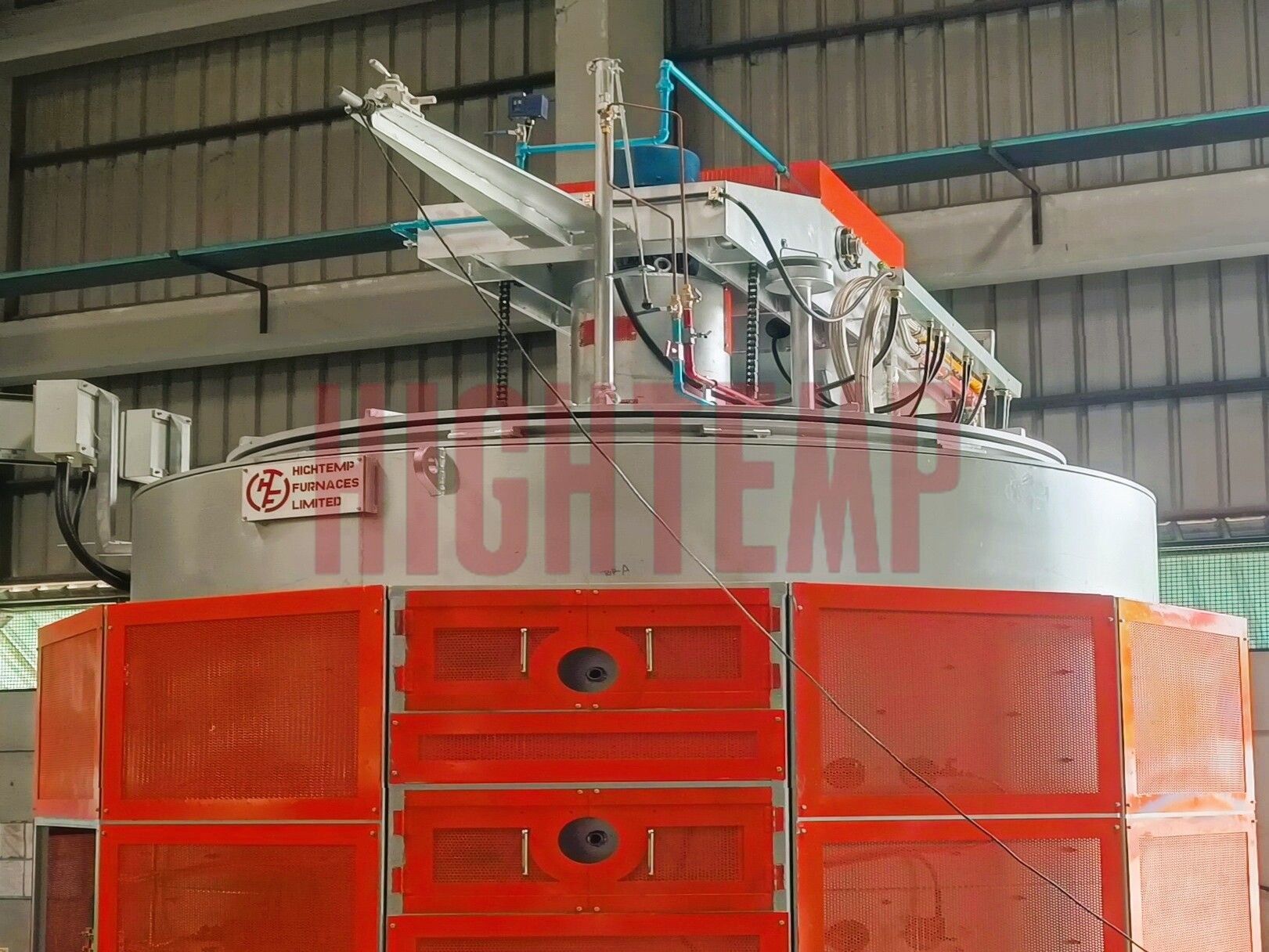
Pit Type Hardening Furnace
HIGHTEMP's Pit Type Hardening Furnace is a reliable and robust heat treatment solution designed for the hardening process, which strengthens metal components by heating them to high temperatures followed by controlled quenching. Operating at temperatures typically ranging from 850°C to 950°C, this furnace ensures uniform heat penetration, making it ideal for long, cylindrical, or heavy components such as shafts, spindles, gears, and axles. The vertical, pit-type design allows efficient processing of components that require deep hardening while maintaining structural integrity. Widely used in automotive, aerospace, and heavy engineering industries, HIGHTEMP’s Pit Type Hardening Furnace delivers consistent results, durability, and energy efficiency, meeting the highest industry standards.
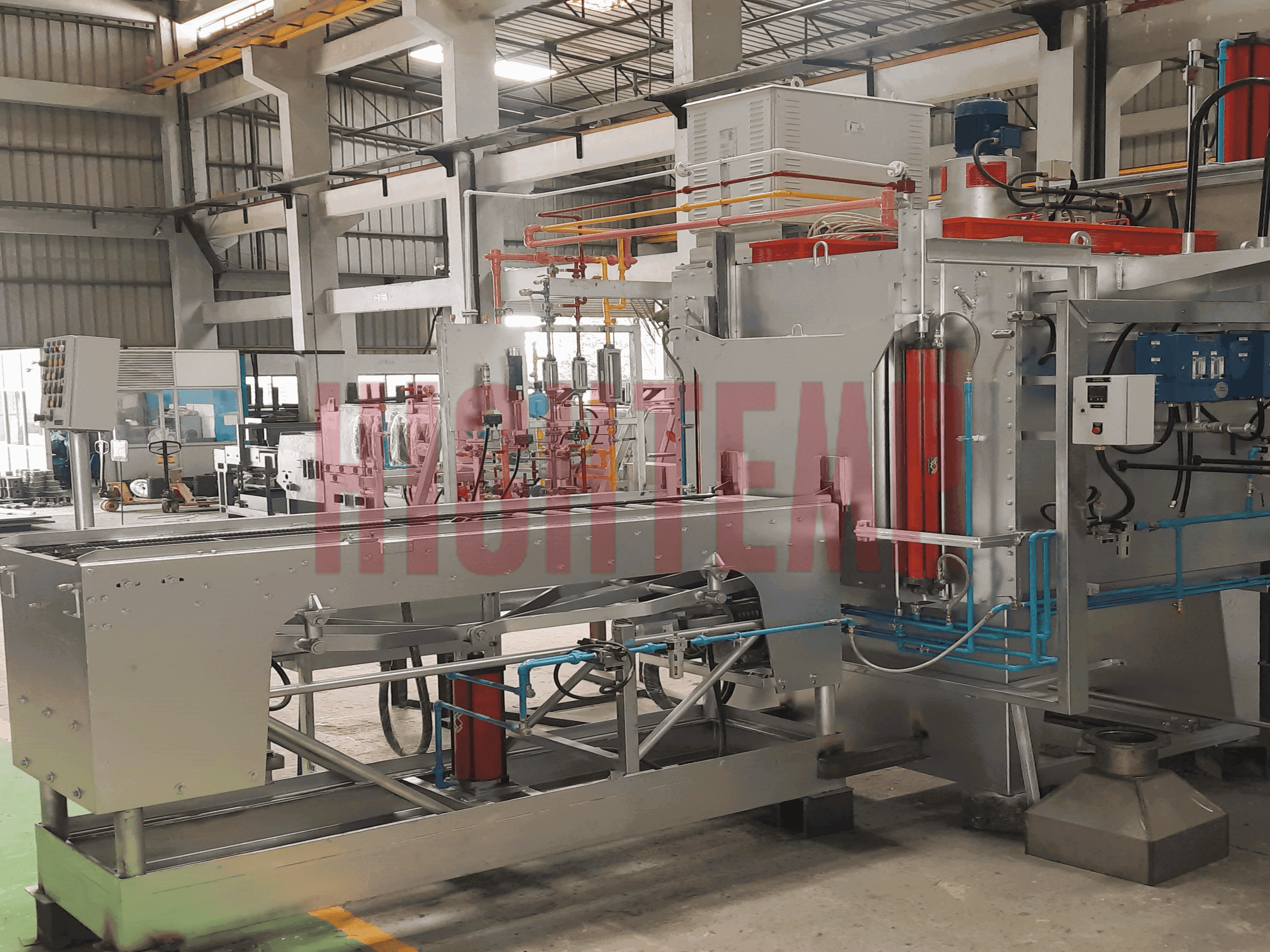
TKM 80
Our Sealed Quench Furnace is ideal for the heat treatment of components like gears, shafts, crankshafts, pins, bolts, fasteners, and tool & die parts. It offers a controlled environment for carburising processes, which are critical for enhancing the mechanical properties of materials such as EN8, EN9, EN19, EN24, 16MnCr5, 20MnCr5, SAE 8620, and EN31. Carburising is used to add carbon to the surface of low-carbon steels to enhance their hardness and wear resistance, while keeping the core material tough and ductile. After carburising, tempering is performed to reduce brittleness and improve the toughness of the hardened surface. It also helps relieve internal stresses that may result from the quenching process. This furnace can perform other heat treatment processes, including hardening, carbonitriding, normalizing, nitrocarburizing, nitriding, austempering, neutral hardening, annealing, and bright hardening.
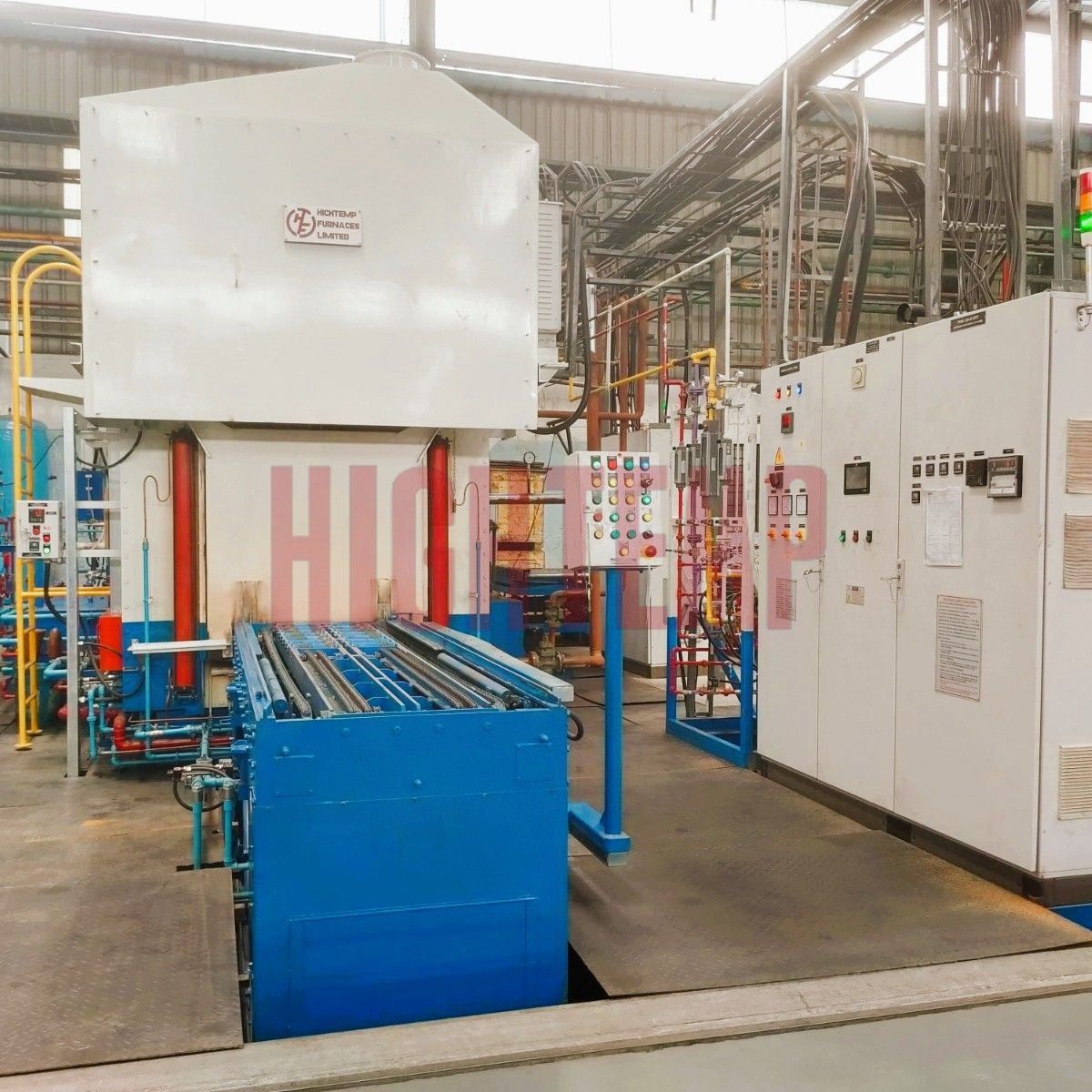
TKM 100
HIGHTEMP Sealed Quench Furnace is the ideal solution for the carbonitriding and tempering of high-performance components, ensuring enhanced surface hardness, wear resistance, and toughness. This furnace is particularly effective for components such as gears, shafts, pins, bolts, fasteners, crankshafts, tool & die parts, and bearings. Using materials like EN8, EN9, EN19, EN24, 16MnCr5, 20MnCr5, SAE 8620, and EN31 (high-carbon steels), it ensures consistent, superior-quality heat treatment. Carbonitriding is a surface hardening process where carbon and nitrogen are diffused into the steel surface, improving its hardness, wear resistance, and fatigue strength. The sealed quench furnace ensures a controlled atmosphere to minimize oxidation and decarburisation. After carbonitriding, tempering is used to relieve internal stresses and reduce brittleness while retaining the hardness of the treated surface. This furnace can perform other heat treatment processes, including carburizing, hardening, normalizing, nitrocarburizing, nitriding, austempering, neutral hardening, annealing, and bright hardening.
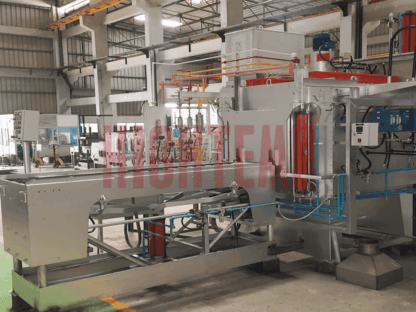
Integral Batch Sealed Quench Furnace
Sealed Quench Furnace (SQF) is used for high-precision heat treatment primarily in auto components industry. This allows heat treatment for carbon steel to reach the desired hardness and strength. The furnace feature allows the materials to be processed in batches rather than continuous operation. HIGHTEMP is the leading manufacturer of Sealed Quench Furnace in India that provides a global clientele, with sales volume exceeding 500+.
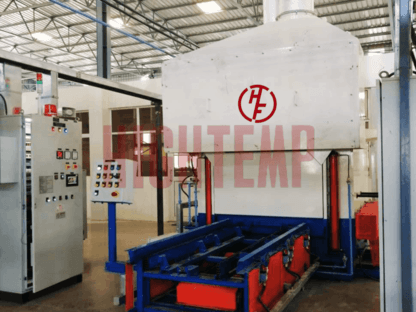
Chamber Furnace
HIGHTEMP's Chamber Furnace is a reliable solution for batch heat treatment, offering excellent temperature uniformity and precise control. Its robust design ensures durability and consistent performance, making it suitable for various applications. The furnace is engineered for efficiency, delivering high-quality results with optimal energy usage.
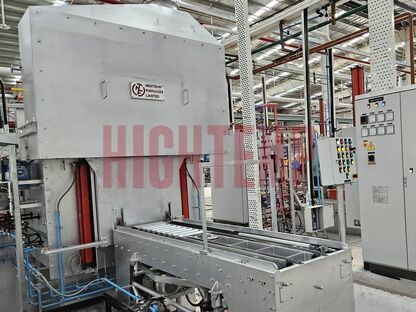
Batch Furnace
HIGHTEMP offers advanced Batch Furnace solutions, designed to meet the specific heat treatment needs of various industries. Our Batch Furnaces provide reliable and uniform heat treatment for a range of materials, ensuring superior quality and durability. Our models include Roller Driven Batch Furnace, Two Tray Roller Hearth Carburising and Hardening Furnace, and Carburising and Hardening Furnace, offering flexibility and optimal performance.
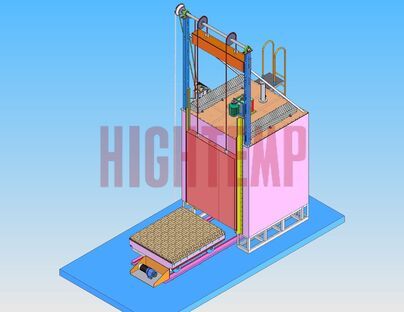
Bogie Hearth Furnace
HIGHTEMP's Bogie Hearth Furnace is designed for the heat treatment of heavy and large components. Equipped with a bogie, the furnace simplifies the loading and unloading process, making it ideal for applications requiring precision and uniform heating. The insulation and efficient heating systems ensure energy savings while maintaining superior performance. This furnaces can be customized with single or double doors and single or double bogies to meet specific user requirements. Materials are loaded onto the bogie using an EOT crane or mechanical devices, and the loaded bogie is moved into the furnace via an electro-mechanical rack-and-pinion or rope-and-drum bogie drive mechanism, ensuring smooth and efficient operation.