At Hightemp Furnaces Limited, we specialize in carburizing, a critical process for improving the surface hardness, core toughness, and wear resistance of steel components. During carburizing, parts are exposed to a carburizing atmosphere at temperatures between 900–950ºC. Following this, the parts are rapidly quenched in oil, resulting in a hardened surface. This treatment significantly enhances the metallurgical properties of the steel, offering superior strength, wear resistance, and toughness.
Our advanced heat treatment furnaces ensure the efficient diffusion of carbon into the surface layer, creating a tough, wear-resistant exterior while maintaining a ductile, impact-resistant core. The carburizing process typically produces a surface layer with a carbon content of about 0.1 to 1.5 mm in thickness.
Carburizing is ideal for components such as Pinion, Pulley, Relay Case, Sleeve/Driver, Free Running Pully, Magnet Core, Rotor, Spark Plug Housing, Hub, Steering Races, Swivel Head, Driver, Pole Shoe,
Bush Presure Disc, Body Tube and other high-stress parts. At Hightemp Furnaces Limited, our carburizing solutions guarantee superior performance, improved core toughness, and increased component longevity.
Industries Served:

Defense Industry

Auto components Industry

Aerospace Industry
Here Are Some Key Items
That Benefit From This Process:
- Gears
- Shafts
- Camshafts
- Crankshafts
- Sprockets
- Bearing Races
- Pins and Linkages
- Valve Seats
- Couplings
- Splines
- Drive Plates
- Rocker Arms
- Dies and Molds
- Machine Tools
- Pinion
Carburising these components ensures a hard, wear-resistant surface while maintaining a tough, impact-resistant core, crucial for their optimal performance in demanding applications.
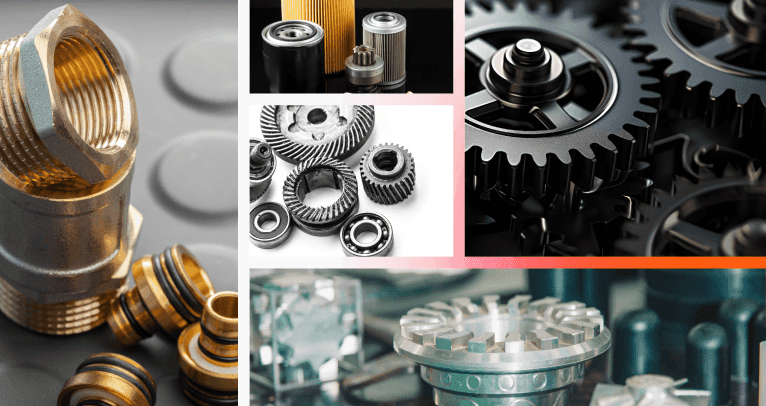
Material Grades That Can Undergo The
Carburising
Material
Carbon Steel, Alloy Steel
Material Grade
AISI 1010, AISI 1015, AISI 1018, AISI 1020, AISI 1025, AISI 1030, AISI 1045, AISI 1060, AISI 3115, AISI 3310, AISI 4320, AISI 8620, AISI 4130, AISI 4140, AISI 4340, 8620, 9310
Carburising Furnaces
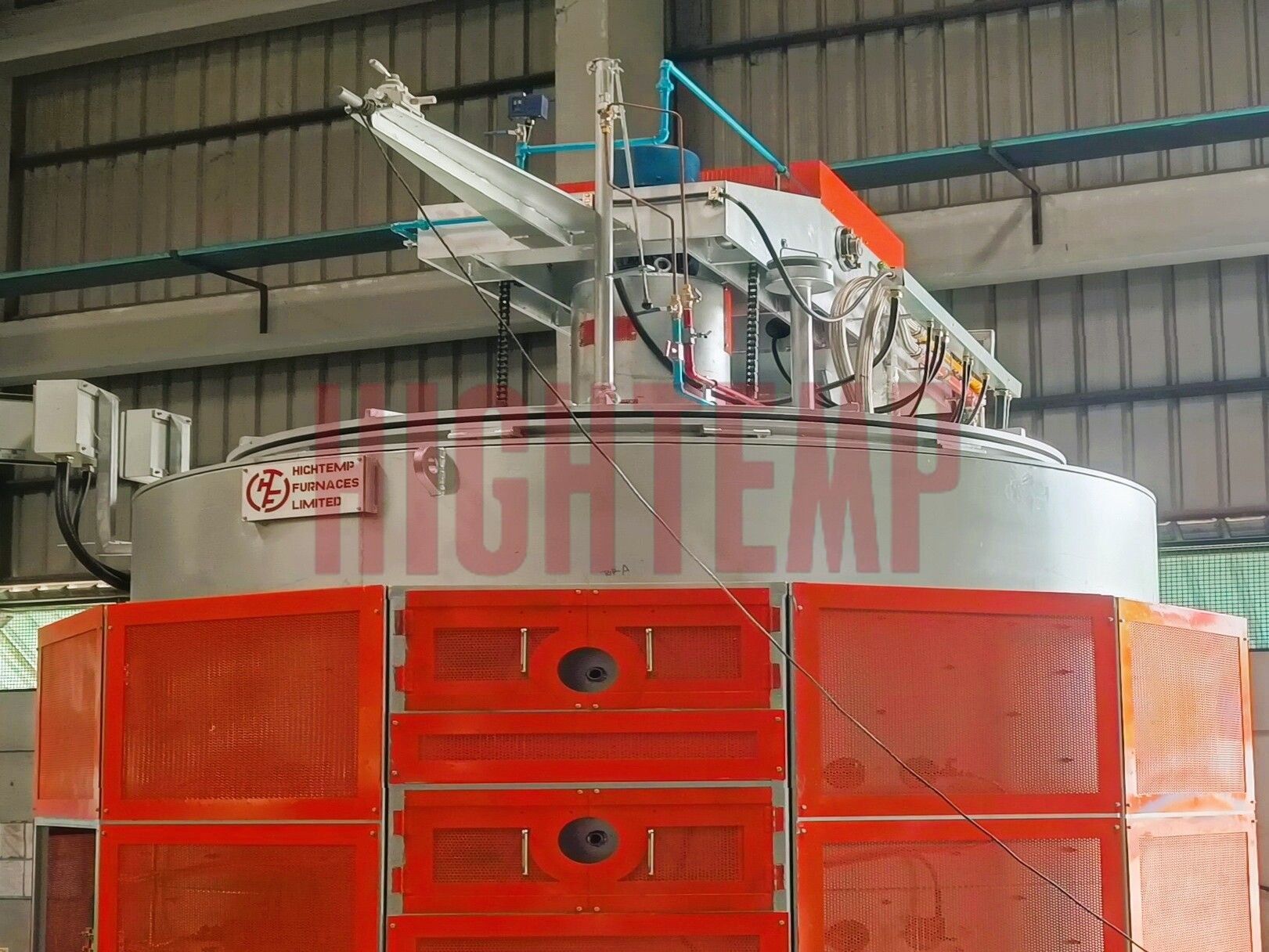
Pit Type Gas Carburising Furnace
HIGHTEMPs Pit Type Gas Carburising Furnace is a specialized heat treatment solution designed for the gas carburising process, where carbon is diffused into the surface layer of steel components to enhance their hardness and wear resistance. Operating at temperatures typically ranging from 850°C to 950°C, our furnace ensures precise control over carburising depth and temperature uniformity. The vertical, pit-type design is ideal for treating long or large components such as shafts, gears, spindles, and axles, making it widely used in industries like automotive, aerospace, and heavy engineering. The furnace operates under a controlled atmosphere, ensuring consistent results and superior surface properties while maintaining core toughness.
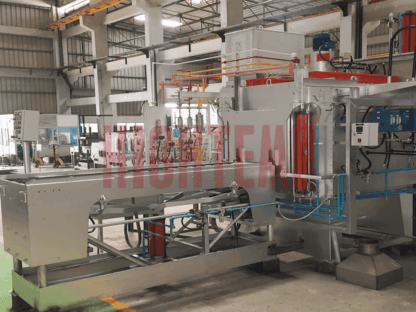
Integral Batch Sealed Quench Furnace
Sealed Quench Furnace (SQF) is used for high-precision heat treatment primarily in auto components industry. This allows heat treatment for carbon steel to reach the desired hardness and strength. The furnace feature allows the materials to be processed in batches rather than continuous operation. HIGHTEMP is the leading manufacturer of Sealed Quench Furnace in India that provides a global clientele, with sales volume exceeding 500+.
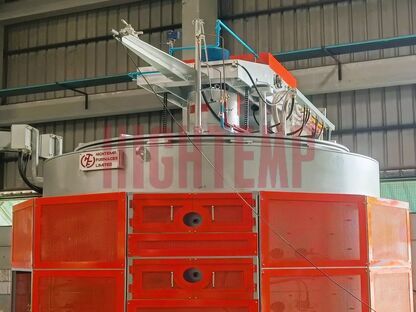
Pit Type Furnace
Pit Furnace, also known as Pit-type Furnace, is an Industrial furnace used for heat treatment processes such as annealing, tempering, and hardening. The Pit Furnace is designed as a deep vertical cylindrical or rectangular chamber which can accommodate various sizes and shapes of materials. HIGHTEMP’s Pit Furnace is typically installed in a pit or deep chamber either below ground level or at ground level, which allows for easy loading and unloading of components.