- Improved Fatigue Strength: The combination of carburising and tempering results in components that are resistant to fatigue and wear.
- Dimensional Stability: The sealed quenching process reduces distortion and warping, maintaining the precision of treated parts.
- Cost-Effective: The furnace’s efficiency optimizes energy use, making it an economical solution for large-scale production.
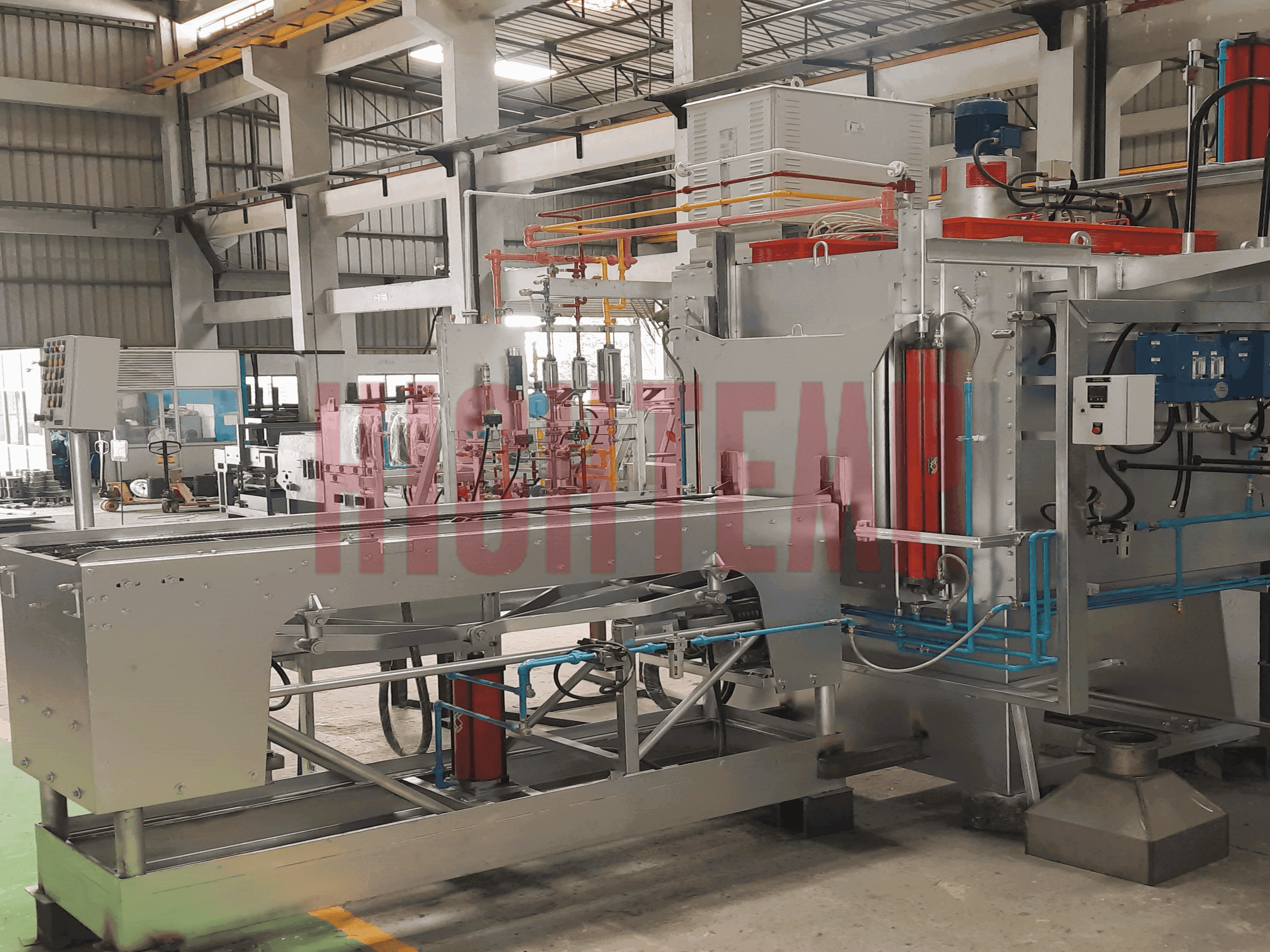

A sealed quench furnace is a highly efficient, controlled atmosphere furnace designed for heat treatment processes such as hardening and tempering. It is widely used in the automotive and industrial sectors for components requiring superior mechanical properties and wear resistance. For the heat treatment of engine components such as connecting rods and valves made from materials like 4130, 4340, 42CrMo4, En-8D, A217, and A351 Hardening and Tempering process is implemented where the components are heated to their austenitizing temperatures in a controlled atmosphere to prevent oxidation and decarburization. Rapid quenching in oil or polymer quenchants, to achieve desired hardness and microstructure. Components are further reheated below the critical temperature to achieve the required toughness, ductility, and stress relief. This furnace can perform other heat treatment processes, including carburizing, , carbonitriding, normalizing, nitrocarburizing, nitriding, austempering, neutral hardening, annealing, and bright hardening..
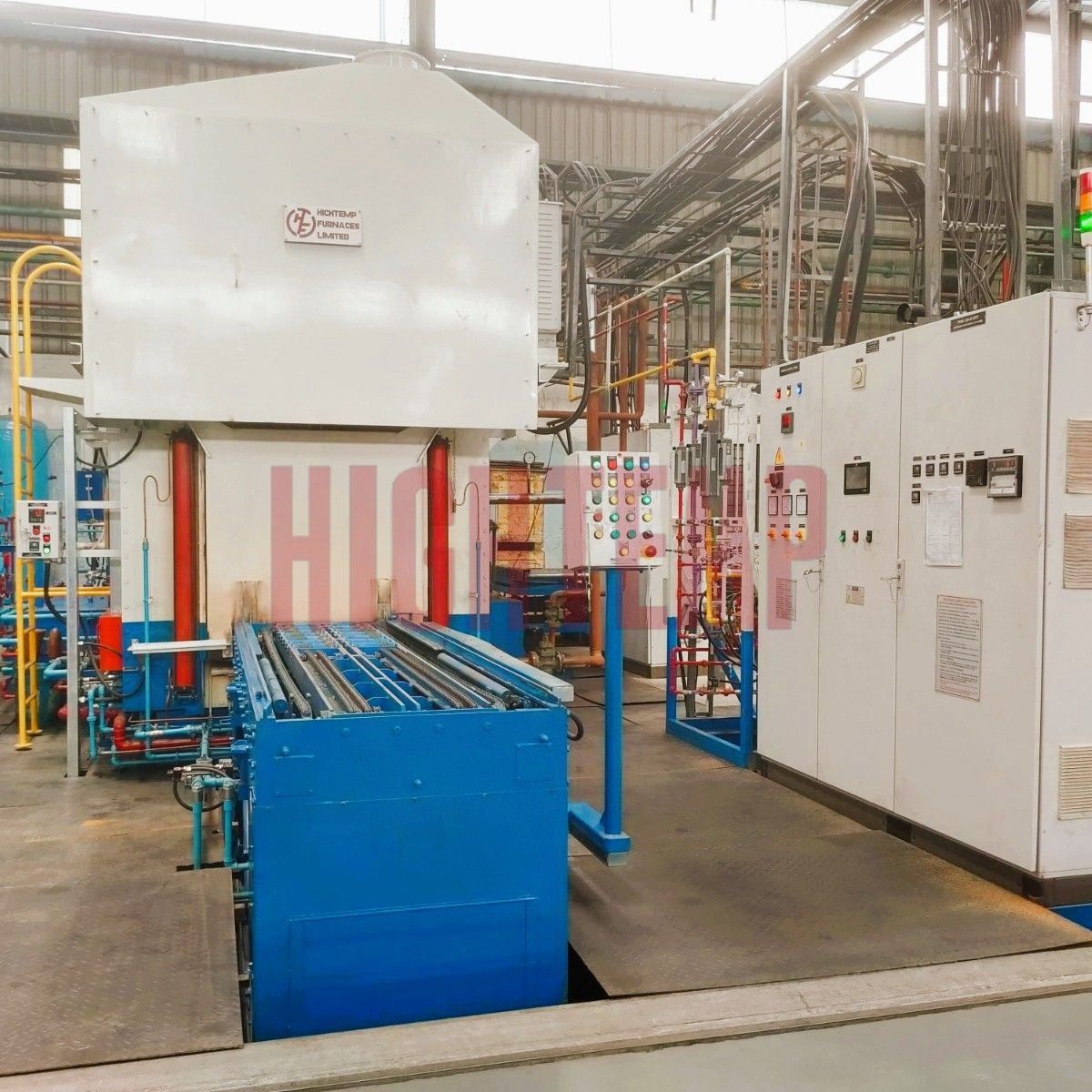

HIGHTEMP Sealed Quench Furnace is the ideal solution for the carbonitriding and tempering of high-performance components, ensuring enhanced surface hardness, wear resistance, and toughness. This furnace is particularly effective for components such as gears, shafts, pins, bolts, fasteners, crankshafts, tool & die parts, and bearings. Using materials like EN8, EN9, EN19, EN24, 16MnCr5, 20MnCr5, SAE 8620, and EN31 (high-carbon steels), it ensures consistent, superior-quality heat treatment. Carbonitriding is a surface hardening process where carbon and nitrogen are diffused into the steel surface, improving its hardness, wear resistance, and fatigue strength. The sealed quench furnace ensures a controlled atmosphere to minimize oxidation and decarburisation. After carbonitriding, tempering is used to relieve internal stresses and reduce brittleness while retaining the hardness of the treated surface. This furnace can perform other heat treatment processes, including carburizing, hardening, normalizing, nitrocarburizing, nitriding, austempering, neutral hardening, annealing, and bright hardening.
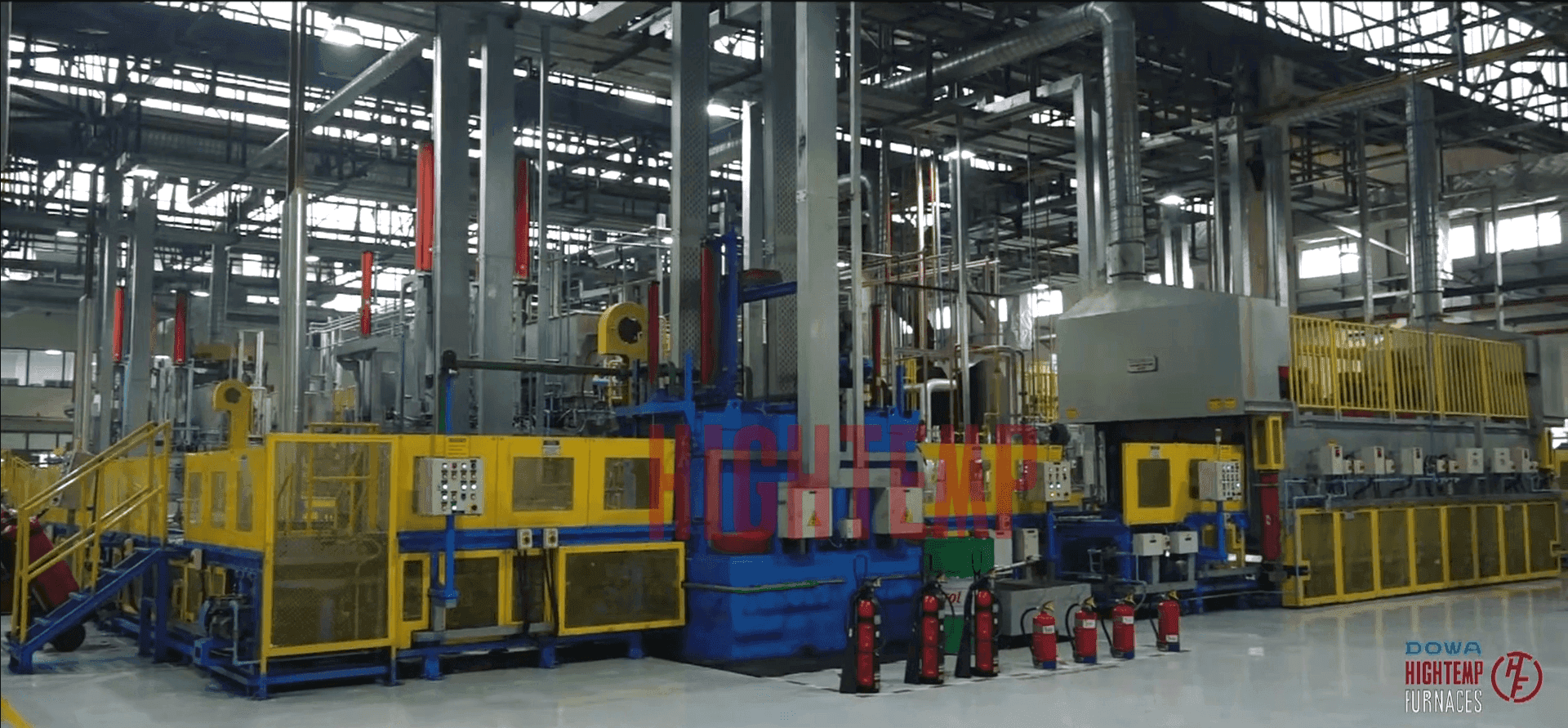

The HIGHTEMP Continuous Gas Carburising Furnace is an advanced heat treatment solution designed for high-volume production and precise carburising of components. Built for efficiency and consistency, this furnace uses a continuous single-track design, making it ideal for industries that demand superior quality, cost-effective operations, and high throughput. Operating at temperatures of up to 950°C, the furnace introduces carbon into the surface layer of steel components to improve hardness, wear resistance, and fatigue strength, while maintaining a tough core. With options for endothermic gas or nitrogen-methanol atmospheres, it ensures optimal carburising conditions tailored to specific requirements.