- Processes 150 kg/hr to 400 kg/hr based on cycle time, ensuring continuous and efficient operations for large-scale production.
- Offers gas-fired or electric heating systems, optimizing energy consumption and reducing operating costs.
- Fully automated PLC-controlled system minimizes manual intervention, ensuring reliable and repeatable operations.
- Modular construction allows flexibility for specific production needs while simplifying maintenance.
- Advanced quenching system ensures uniform cooling, enhancing mechanical properties of treated components.
- Pneumatic doors ensure secure sealing and minimize operational risks during furnace operation.
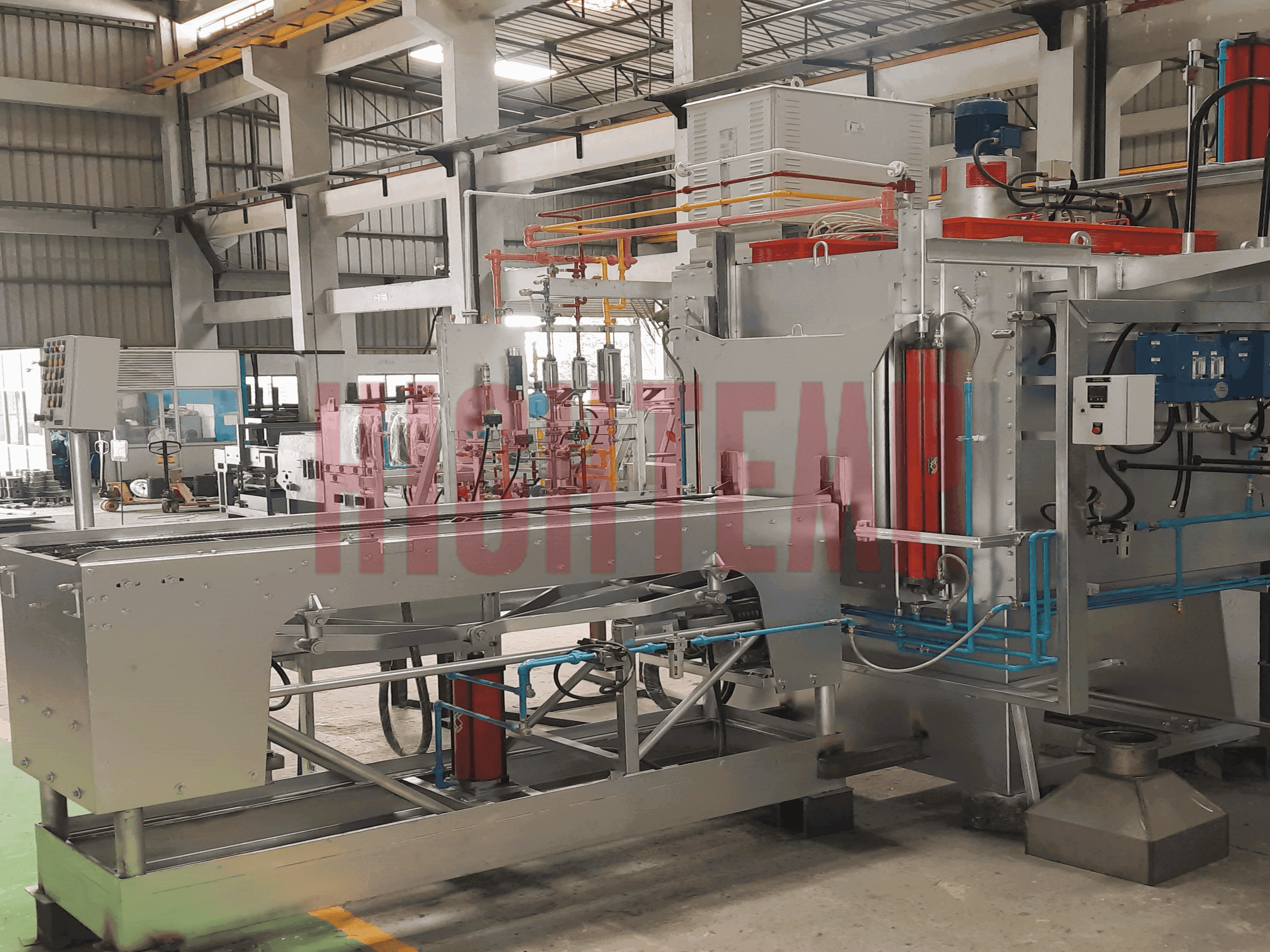

Our Sealed Quench Furnace is ideal for the heat treatment of components like gears, shafts, crankshafts, pins, bolts, fasteners, and tool & die parts. It offers a controlled environment for carburising processes, which are critical for enhancing the mechanical properties of materials such as EN8, EN9, EN19, EN24, 16MnCr5, 20MnCr5, SAE 8620, and EN31. Carburising is used to add carbon to the surface of low-carbon steels to enhance their hardness and wear resistance, while keeping the core material tough and ductile. After carburising, tempering is performed to reduce brittleness and improve the toughness of the hardened surface. It also helps relieve internal stresses that may result from the quenching process. This furnace can perform other heat treatment processes, including hardening, carbonitriding, normalizing, nitrocarburizing, nitriding, austempering, neutral hardening, annealing, and bright hardening.
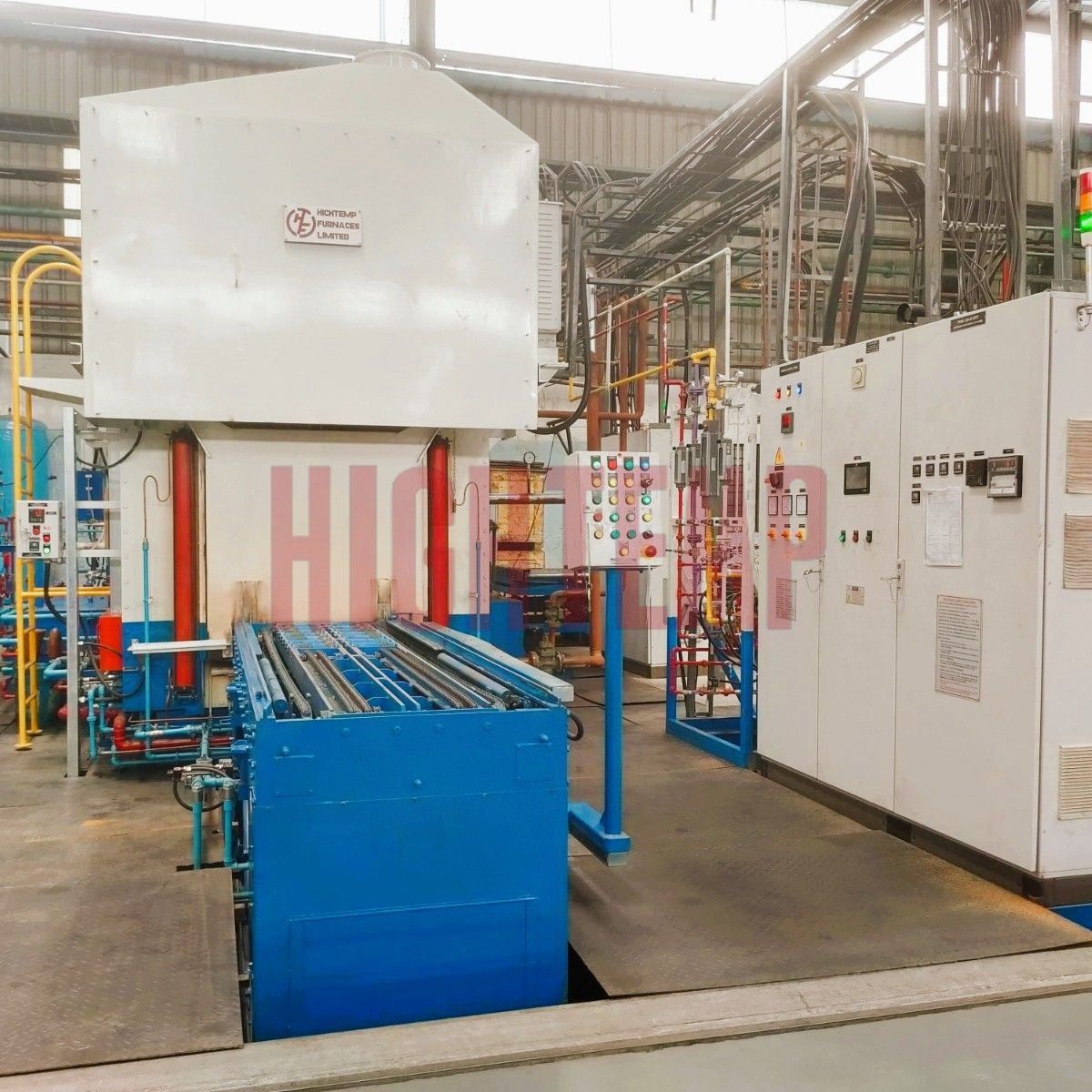

HIGHTEMP Sealed Quench Furnace is the ideal solution for the carbonitriding and tempering of high-performance components, ensuring enhanced surface hardness, wear resistance, and toughness. This furnace is particularly effective for components such as gears, shafts, pins, bolts, fasteners, crankshafts, tool & die parts, and bearings. Using materials like EN8, EN9, EN19, EN24, 16MnCr5, 20MnCr5, SAE 8620, and EN31 (high-carbon steels), it ensures consistent, superior-quality heat treatment. Carbonitriding is a surface hardening process where carbon and nitrogen are diffused into the steel surface, improving its hardness, wear resistance, and fatigue strength. The sealed quench furnace ensures a controlled atmosphere to minimize oxidation and decarburisation. After carbonitriding, tempering is used to relieve internal stresses and reduce brittleness while retaining the hardness of the treated surface. This furnace can perform other heat treatment processes, including carburizing, hardening, normalizing, nitrocarburizing, nitriding, austempering, neutral hardening, annealing, and bright hardening.
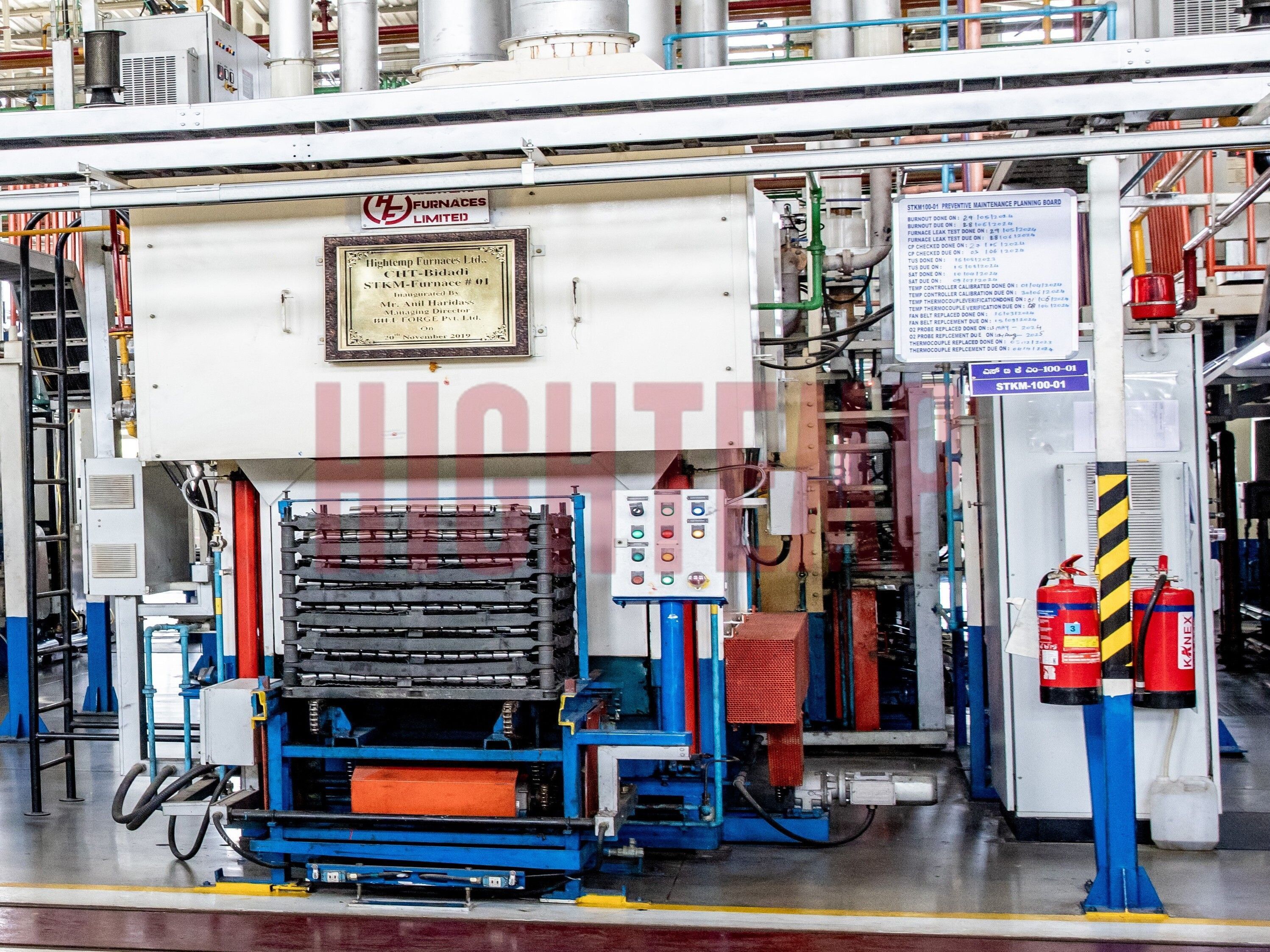

The Semi-Continuous Sealed Quench Furnace by HIGHTEMP provides an advanced heat treatment solution for carbonitriding/carburising and tempering, designed to enhance the wear resistance, surface hardness, and toughness of critical components such as gears, shafts, crankshafts, pins, bolts, fasteners, and bearings, and is compatible with a variety of material grades, including Medium- Carbon Steels like EN8, EN9, Alloy Steels such as EN19, EN24, SAE 4140, Low-Alloy Steels like 16MnCr5, 20MnCr5, SAE 8620, and High-Carbon Steels like EN31, making it the ideal choice for industries such as automotive, aerospace, heavy machinery, and precision engineering, where superior performance, durability, and reliability are crucial for high-stress, high-performance applications.